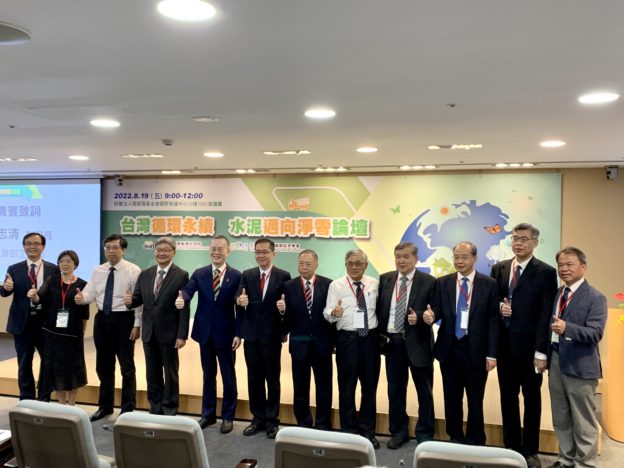
台灣營建研究院與台灣循環經濟學會今日舉辦「台灣循環永續,水泥邁向淨零論壇」,會中以提高替代原料與燃料比率是水泥產業減碳大方向,並以國際的 5C(熟料、水泥、混凝土、營建、碳化)策略,作為台灣水泥產業的借鏡,而台泥和亞泥也在會中分享低碳水泥的發展方向與目標。
台灣永續能源研究基金會董事長簡又新表示,各國陸續宣示 2050 淨零碳排,水泥產業因為製程特性,能源使用和碳排放量較高,碳排量約占全球排放量的 7%,全球水泥與混凝土協會(GCCA)提出 2050 年水泥和混凝土的淨零排放的路徑圖,承諾 10 年內將混凝土碳排量減少 25%。
行政院環保署副署長沈志修表示,2050 淨零碳排是必須要做的轉型,雖然水泥產業有優勢存在,但製造過程產生廢棄物必須處理,關鍵在於資源循環,作為水泥的燃料是一定要走的路,因此環保署成立「資源循環辦公室」,期望帶動台灣低碳水泥的發展。
台灣循環經濟學會理事長呂良正分享,歐盟通過 CBAM 碳邊界調整機制法規,預計 2026 年正式實施,未來歐盟對進口到當地的碳密集型產品,將依據碳排量,進口商必須完成採購相對應的 CBAM 憑證,因此尋找水泥的替代原料、替代燃料已經成為國際趨勢。
參照各國的做法,呂良正表示,日本水泥產業 2020 年生產每噸水泥已經可以去化 460 公斤的廢棄物,台灣目前僅 200 多公斤,而美國則用回收材料替代原材料生產低碳水泥和混凝土,至於德國則用粉碎混凝土當作碎石和沙子的替代原料。
呂良正指出,目前日本水泥業減碳趨勢採用的卜特蘭水泥,主要是由氧化鈣、氧化矽、氧化鋁和氧化鐵 4 種氧化物組成,取自大理石、黏土、矽礦、鐵礦砂等原料,因此善用含 4 種元素的廢棄物,可以用來替代天然礦石。
呂良正強調,全球水泥產業的中期減碳目標是 2030 年前,增加熱料替代飛灰、煅燒粘土、水淬高爐爐渣粉和石灰石粉,長期目標則是 2050 年前,減量 38 億噸碳排量,透過生產熟料的節省、混凝土生產的效率、水泥和膠結材料的節省、再碳化、碳捕捉利用、設計和施工的效率的 5C 策略,以及電力的去碳化來實行。
台泥副總經理王建全分享,水泥的工藝製程已到極限,台泥熱效率更是做到亞洲第一,勝過歐洲和日本的水泥,但是因為受到很多標準規範和使用限制,達到 2050 淨零碳排的過程中,所有減碳都必須符合「經濟可行性」和「市場接受度」,否則怎麼減碳都沒有用。
王建全表示,水泥產業的減碳方法有很多,像是非洲水泥廠有新型的煅燒粘土,但是為什麼台灣無法使用,因為減碳不是喊口號,所以必須因地制宜,若是台灣使用非洲的替代燃料,但是因為運輸產生更多碳排,那就沒有意義。
王建全指出,水泥為台灣十大排碳產業之一,主要碳排來自前段原料、燃料與窯爐製程,目前亟需減碳的原料和燃料替代,並改善製程技術,以及相關法規的訴求,像是 CNS 61 水泥國家標準規定卜特蘭水泥總添加物函令必須小於 5%,但在去年放寬到 10%,便是有利循環經濟的對策。
談到低碳水泥的發展,亞泥副總經理張志鵬分享,水泥具有滯留時間長、溫度高、攪拌力強三大優勢,可以讓所有廢棄物調配成水泥,但台灣水泥業減碳的速度比較慢,主要是跟政府和法規有關,但是導入循環經濟的環境效益高,包括使用替代燃料和原料降低碳排、減少開採天然原料和燃料耗用需求,並為政府及產業解決廢棄物處理問題。
張志鵬表示,亞泥積極推廣低碳水泥的使用,目前觀察國際做法之後,目標三年就可望與國際接軌,而且目前是台灣唯一生產低碳墁砌水泥和卜特蘭石灰石的水泥業者,同時積極研發碳捕捉再利用,期望透過低碳製程做到低碳混凝土和負碳混凝土。
為加速低碳水泥的發展,張志鵬建議,政府應帶頭使用低碳水泥,鼓勵公共工程採購,並加以調整不利於低碳產品使用的稅制,例如一般較高排碳的卜特蘭水泥貨物稅每噸 320 元,而其他低熟料占比的墁砌水泥、混合水泥貨物稅 440 元反而較高,實不利低碳水泥的推廣。
(首圖來源:科技新報)